در این مقاله قصد داریم تا به بررسی تمام جزئیات مرتبط با مواد اولیه تولید فولاد و روش های تولید فولاد بپردازیم. اگرشما نیز در این زمینه فعالیت می کنید و یا به این موضوع علاقه دارید بهتر است تا پایان این مقاله همراه ما باشید. زیرا می خواهیم اطلاعات دقیقی در این رابطه به شما ارائه دهیم تا آگاهی شما نسبت به این موضوع افزایش یابد.
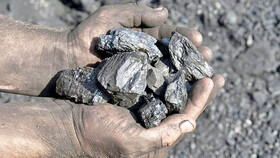
ماده اولیه اصلی: سنگ آهن مگنتیت
می توان گفت سنگ آهن مگنتیت یکی از مشتقات سنگ آهن می باشد. خاصیت آهنربایی این سنگ توانسته است آن را بسیار خاص کند. این ماده را می توان جزو اولین مواد معدنی مغناطیسی در سطح کره زمین دانست. همچنین این سنگ جزو اولین آهنربا جهان نیز می باشد. می توان مگنتیت را یکی از با ارزش ترین مشتقات سنگ آهن به حساب آورد که از آن به وجود می آید.
پیشنهاد مطالعه: درباره سنگ آهن چه میدانید؟! از شناسایی تا استخراج سنگ آهن + ویدیو و عکس
رنگ این سنگ ها تیره می باشد و اغلب به شکل بلور وجود دارند. این نوع سنگ بسیار نادر و کمیاب می باشد و از آن در تولید آهنربا استفاده می شود. این سنگ در ظاهر به شکل یک هشت وجهی می باشد که به صورت دو هرم از قاعده به هم وصل شده هستند.
بررسی و مقایسه مواد اولیه تولید فولاد
می توان گفت مواد اولیه تولید فولاد متفاوت می باشند. خود این فلز از آهن و کربن تشکیل شده است. مواد تشکیل دهنده فولاد تخصصی می باشند. به طور کلی این محصول از دو درصد کربن تشکیل شده است. همچنین یک درصد ازمنگنز و درصد کمی از اکسیژن، فسفر، سولفور، سیلیکون تشکیل شده است. شاید نام فولاد را زیاد شنیده باشید. این محصول جزو مواد اولیه مهم در صنعت به حساب می آید و در قسمت های مختلف از آن استفاده می شود. همانطور که گفته شد فولاد از یک عنطر ساخته نشده است و از چندین عنصر مختلف در کنار هم به وجود می آید. تمام این عناصر در صورت ترکیب ماده ای به نام فولاد را به وجود می آورند. از این محصول در ساخت ابزار آلات نیز بسیار استفاده می شود.

ترتیب و مراحل اضافه شدن هر ماده در کوره
در بالا به مواد اولیه تولید فولاد اشاره کردیم. حال می خواهیم به مراحل ساخته شدن آن درون کوره بپردازیم. یکی از ابتدایی ترین روش ها در تخت فولاد کوره باز می باشد. امروزه روش جدیدی به اسم بسمر در ساخت فولاد ایجاد شده است که یک روش نوین و بسیار کارآمد به حساب می آید. در روش ساخت فولاد به صورت کوره باز، یک کوره سقفی و کم عمق وجود دارد. در این روش سنگ آهن را با کمی قراضه فولادی درون یک کوره ترکیب می کنند. سپس اکسیژن خالص را به صورت مستقیم به داخل کوره می دمند. این کار دمای داخل کوره را افزایش می دهد. قراضه ها در این دما به صورت کامل ذوب می شوند. در این دما کربن نیز تا حد زیادی کاهش پیدا می کند و بستر لازم برای تولید فولاد مایع فراهم می شود. اما روش های دیگری نیز وجود دارند.
فرایند اکسیژن بازی یکی دیگر از این روش ها می باشد. این روش به این صورت است که اکسیژن به داخل منبعی دمیده می شود. در روش کوره بلند اکسید های آهن به عنوان سنگ معدن خام، کلوخه و یا زینترن وارد کوره می شوند. از زمین سنگ خام خارج می شود و آن را به اندازه های مشخصی در می آورند. این سنگ های استخراج شده هماتیت یا مگنتیت می باشند که تا ۷۰ درصد آن ها شامل آهن می باشد. این آهنی که به دست آمده است می تواند به صورت مستقیم درون کوره قرار بگیرد.
مواد اولیه تولید فولاد در کارخانه فولاد و نقش هر یک در فرایند تولید
در این قسمت می خواهیم به معرفی مواد اولیه تولید فولاد بپردازیم. می توان سنگ آهن، زغال سنگ، سنگ آهک و آهن قراضه را جزو مواد اصلی در کارخانه تولید فولاد به حساب آورد. کربن، منگنز، کروم، نیکل، مولیبدن، وانادیم، بور، تیتانیم، سیلیسیم، گوگرد، فسفر، آلومینیوم جزو مهمترین عناصر شیمیایی در تولید فولاد می باشند. به طور کلی برای ساخت فولاد از ۱۵۰ کیلو سنگ آهک، ۱۳۸ کیلوگرم آهن قراضه، ۱۷۲۵ کیلوگرم سنگ آهن، ۶۴۵ کیلوگرم زغال سنگ استفاده می شود. تمام این مواد جزو مواد اولیه تولید فولاد به حساب می آیند. می توان گفت که نبودن هر کدام از این مواد می تواند تاثیرات منفی بر روی تولیدات فولاد بر جای بگذارد.
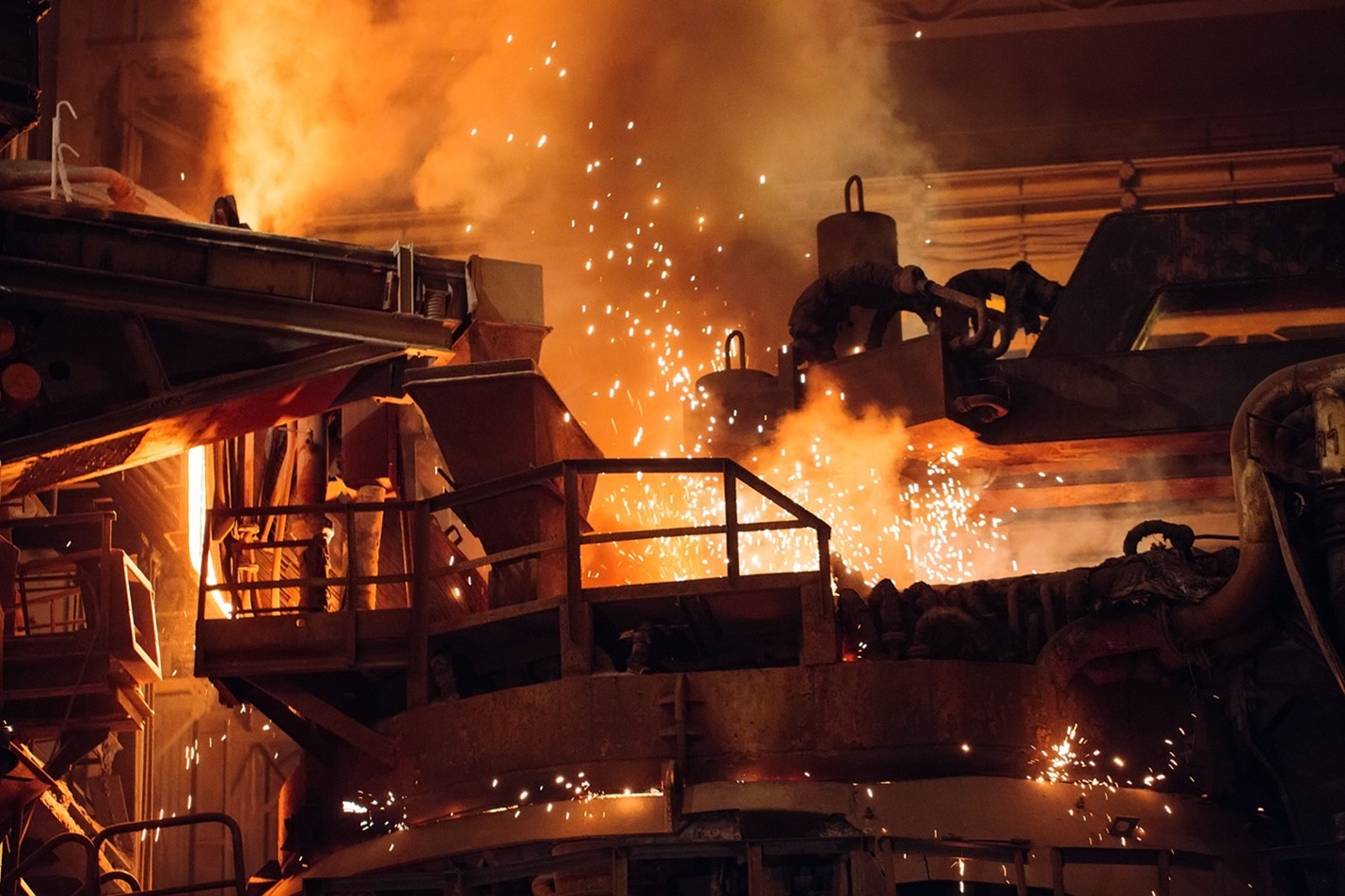
پس بهتر است افرادی که می خواهند از این روش برای تولید فولاد استفاده کنند به طور دقیق با مواد اولیه تولید فولاد و میزان هر کدام آشنایی داشته باشند تا بتوانند به محصول نهایی دست پیدا کنند.
روش های تولید فولاد
در تولید فولاد دو روش کلی وجود دارد. فرایند اکسیژن بازی را می توان جزو یکی از فرایندهای مهم دانست. در این روش اکسیژن را به داخل یک محفظه می دمند و فرآیندی گرماده ایجاد می شود. در این روش یک کوره را با ۳۰ درصد از ضایعات فولاد و آهن مذاب پر می کنند. یک لوله نیزه مانند و باریک را به داخل کوره فرستاده و اکسیژن را با شدت بسیار زیاد به داخل آن می دمند. در این شرایط تمام ناخالصی هایی که درون کوره وجود دارد به اکسید تبدیل می شود. روش بعدی روش کوره قوس الکترونیکی می باشد. در این روش ابتدا تمام ضایعات به داخل کوره با استفاده از یک جرثقیل سقفی وارد می شوند. این ضایعات را از سه منبع کلی تهیه می کنند.
ضایعات خانگی، ضایعات صنعتی، ضایعات کهنه. این نوع کوره از یک سقف متحرک و حمام دوار تشکیل شده است که دارای ۳ الکترود گرافیکی می باشد. می توان گفت این نوع کوره تا حجم ۱۰۰۰ تن فولاد را درون خود جای می دهد. بعد از آن که این ضایعات به طور کامل درون کوره قرار گرفته اند در کوره بسته می شود و الکترود ها نیز درون آن جایگذاری می شوند. قوس الکترونیکی سبب ذوب شدن این ضایعات در کوره می شود. سپس برای اینکه سرباره ایجاد شود مواد زیر به داخل کوره اضافه می گردد. آهک به شکل های مختلف موجود می باشد و کلسیم فلوراید و سنگ آهن، جزو موادی می باشند که به داخل کوره اضافه می شوند.
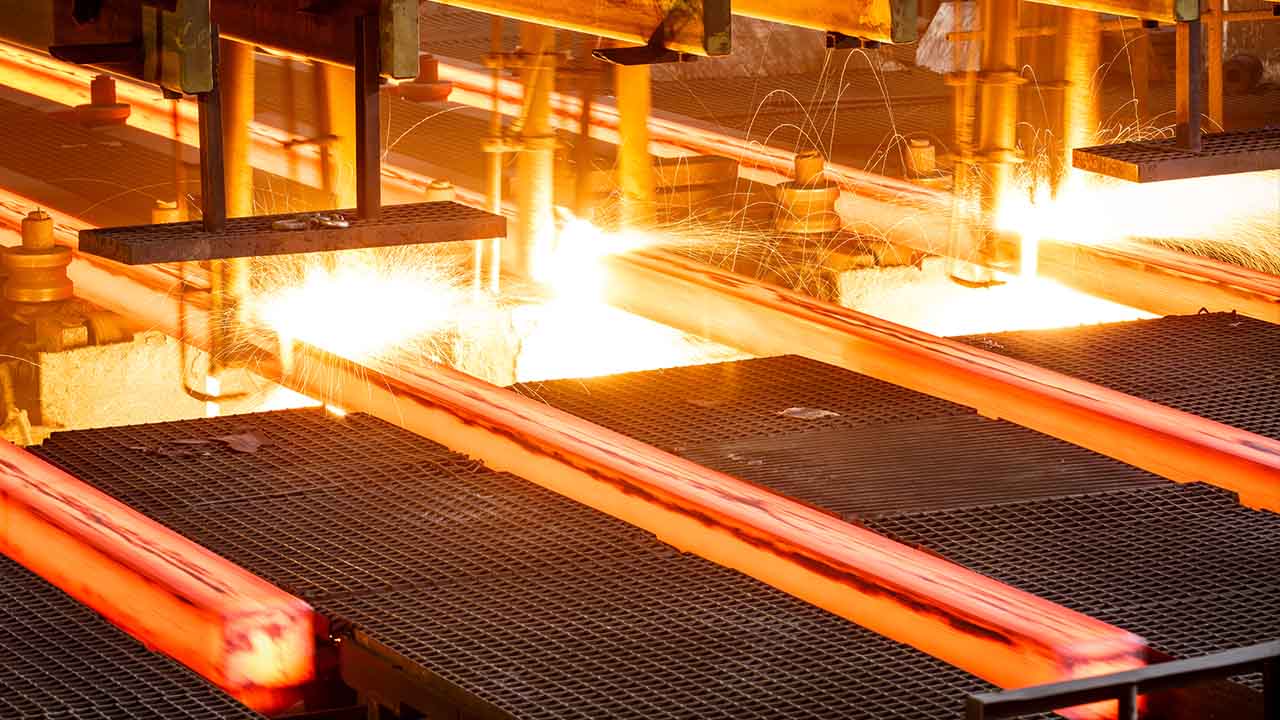
مزایای روش فولادسازی با قوس الکترونیکی
همانطور که اشاره کردیم مواد اولیه تولید فولاد متفاوت می باشند. این مواد در روش های مختلف به فولاد تبدیل می شوند. حال می خواهیم به بررسی مزایا هر کدام از این روش ها بپردازیم. روش کوره قوس الکترونیکی یکی از این روش ها می باشد که قبل تر در مورد آن صحبت کردیم. ساخت فولاد با کیفیت بالا یکی از مزیت های این روش در تولید فولاد می باشد. از دیگرمزایای این روش به تولید زیاد فولاد در یک ذوب می توان اشاره کرد. در هر یک ذوب این کوره ها تا ۱۵۰ تن فولاد درست می شود.
پیشنهاد مطالعه: تولید آهن اسفنجی با قوس الکتریکی
مزایای فولاد سازی به روش اکسیژن قلیایی: این روش را جزو اساسی ترین روش های تولید فولاد سازی به حساب می آورند. کنترل ترکیبات شیمیایی در این روش یکی دیگراز مزیت های آن می باشد که نشان می دهد که ناخالصی هایی مانند فسفر و سیلیکون از آن خارج شده اند. این روش به دلیل مزایایی که دارد یک روش پرطرفدار در سطح دنیا می باشد. اکثر افراد از این روش برای تولید فولاد استفاده می کنند. این نوع روش تولید فولاد توانایی آن را دارد که در کم تر از ۴۰ دقیقه اندازه ۱۲ ساعت کوره آتشدان روباز، فولاد تولید می شود.
می توان گفت که تولید فولاد به صورت کوره بلند یک روش بسیار پرطرفدار می باشد. در این روش اکسید های آهن و ذوب آهن خام احیا می شوند و از ناخالصی ها تفکیک می شوند. این روش نیاز به تاسیسات بسیار مجهز و عظیم دارد. در قسمت بالا تجهیزاتی مانند سنگ آهن، زغال سنگ و سنگ آهک وارد می شوند و از قسمت پایین هوای گرم دمیده می شود. این مواد خام طی ۸ ساعت زمان دارند که به کف کوره برسند. در زمان مشخصی این محصولات مذاب از کوره بیرون می آیند و هوای گرم به اوج خود می رسد. این روش اما کم تر مورد استفاده قرار میگیرد. از معایب این روش می توان هزینه بالای آن را نام برد که در حجم کم تولید فولاد اصلا به صرفه نمی باشد.
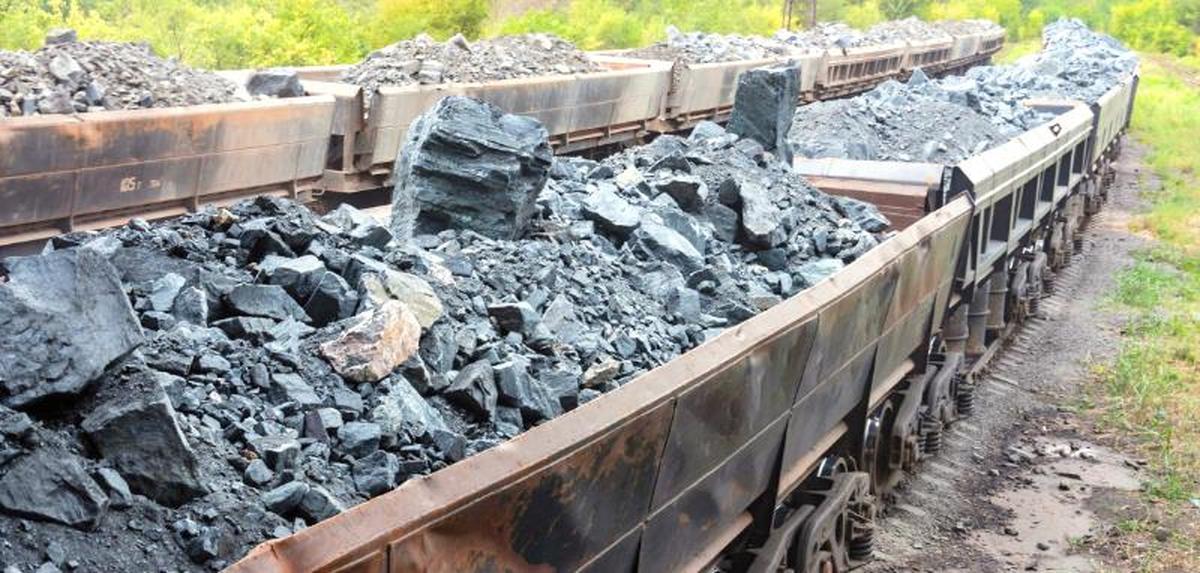
بهترین روش تولید فولاد
روش ذوبی یک روش بسیار پرطرفدار می باشد. در این روش از انواع و اقسام کوره های ذوب آهن استفاده می شود. در این روش آهن خام خارج شده از کوره های بلند را مستقیم وارد کوره قوس الکترونیک و پاتیل می کنند. به این صورت اکسیژن و کربن اضافی آن را می سوزانند و به یک فولاد با کیفیت تبدیل می کنند. امروزه روش های جدیدی برای تولید فولاد استفاده می شود. دیگر به جای حرارت دادن های زیاد که انرژی بالایی نیز صرف می کرد، با استفاده ازگاز ها و افزودنی های مختلف این اکسیژن اضافی را خارج می کنند. همچنین از این روش برای جداسازی مواد دیگر مانند گوگرد و منگنز و … از آهن استفاده می کنند.
این روش بسیار برای تولید فولاد در حجم کم مقرون به صرفه می باشد. همچنین از آهن اسفنجی برای مقرون به صرفه بودن و اقتصادی بودن این کار استفاده می شود. در بالا در رابطه با بهترین روش تولید فولاد صحبت کردیم. حال افراد بر حسب امکاناتی که در اختیار دارند و مقدار حجمی که می خواهند فولاد تولید کنند می توانند یکی از این روش ها را استفاده کنند. تولید فولاد یک کار تخصصی و بسیار حساس می باشد که باید در آن از تجهیزات پیشرفته و افراد متخصص در این زمینه بهره برد تا بتوان بهترین نتیجه ممکن را به دست آورد. امروزه کشور ما نیز با داشتن تجهیزات بسیار عالی در این زمینه توانسته است بسیار در این عرصه پیشتاز باشد. همچنین توانسته است حجم انبوهی از فولاد را تولید کند و کشور را از واردات این محصول بی نیاز سازد.
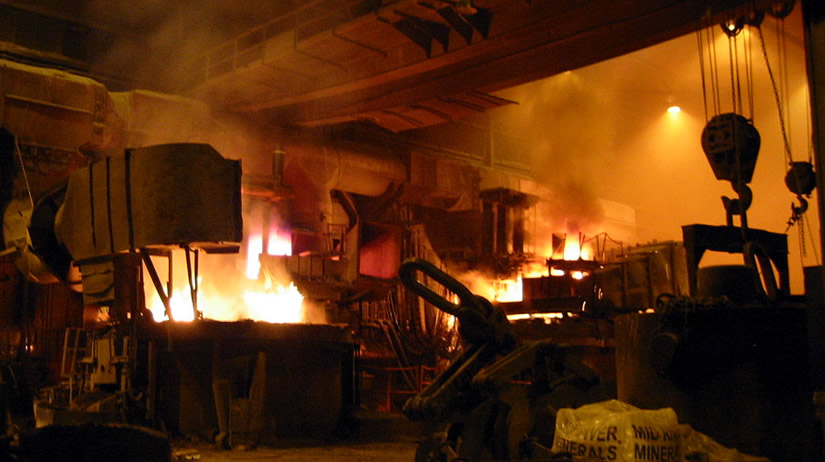
جمع بندی در رابطه با مواد اولیه تولید فولاد
در مطالب بالا سعی کردیم در رابطه با مواد اولیه تولید فولاد و روش های تولید فولاد اطلاعاتی در اختیارتان قرار دهیم. اگر شما به این موضوع علاقه مند هستید و یا در این زمینه فعالیت دارید می توانید از این اطلاعات استفاده کنید و آگاهی خود را در این زمینه افزایش دهید. تولید فولاد یکی از رکن های اصلی در صنعت می باشد. زیرا این ماده در تولید بسیاری از محصولات نقش مهمی دارد. به عنوان مثال می توان از فولاد در تولید ابزار آلات استفاده کرد. استقامت بالای این محصول توانسته است آن را بسیار کارآمد کند. به گونه ای که افراد می توانند از آن در تولید محصولاتی که نیاز به استقامت و مقاومت بالایی دارند استفاده کنند.
امید است با مطالب بالا توانسته باشید اطلاعات مفیدی در این زمینه به دست آورده باشید و بهتر و بیشتر با مواد اولیه تولید فولاد و روش های این کار آشنا شده باشید.